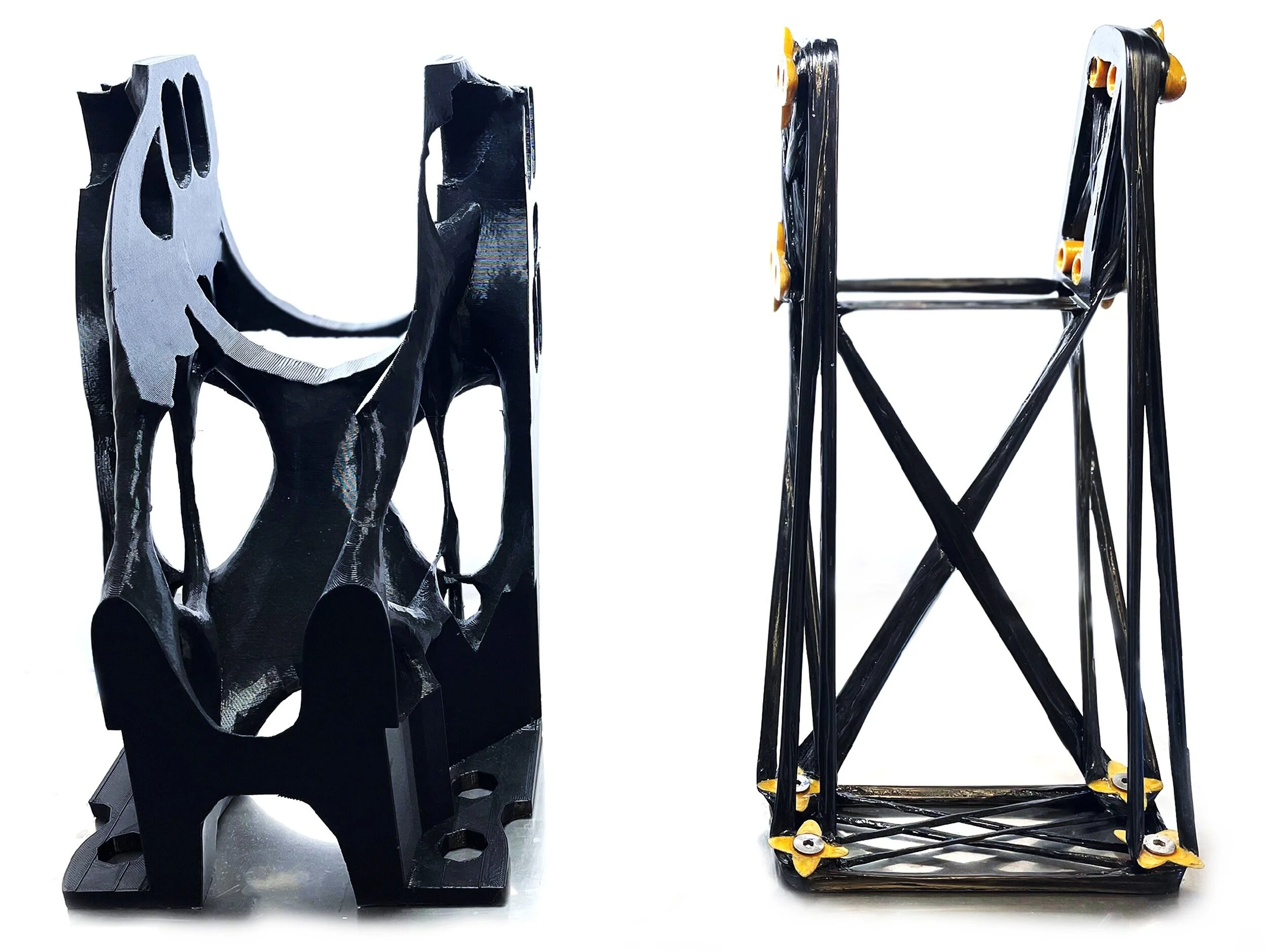
the shuttle brace
AGGRAVATED OPTIMIZATION
OPTIMIZATION
A common strategy in optimization for FEA calculation is load path analysis. The process is based on a solid block in the initial concept is put through a series of tests to take away material (subtraction).
The outcome design can be expensive or impossible to make with standard methodologies. While metal 3d printing has come a long way, it’s not a viable way for mass production due to the fabrication times and costs. By using Gradel’s fiber winding technology the optimization can go one step by using high strength tows and recreating the digital optimized model.
In the case of this bracket a non-consolidated approach was utilized to simplify the optimized model for robotic production.
The 3d printed version in PLA (Image left) took 36 hours to produce. While the fiber wound part (image right) took approx. 45 minutes using robotic fabrication.


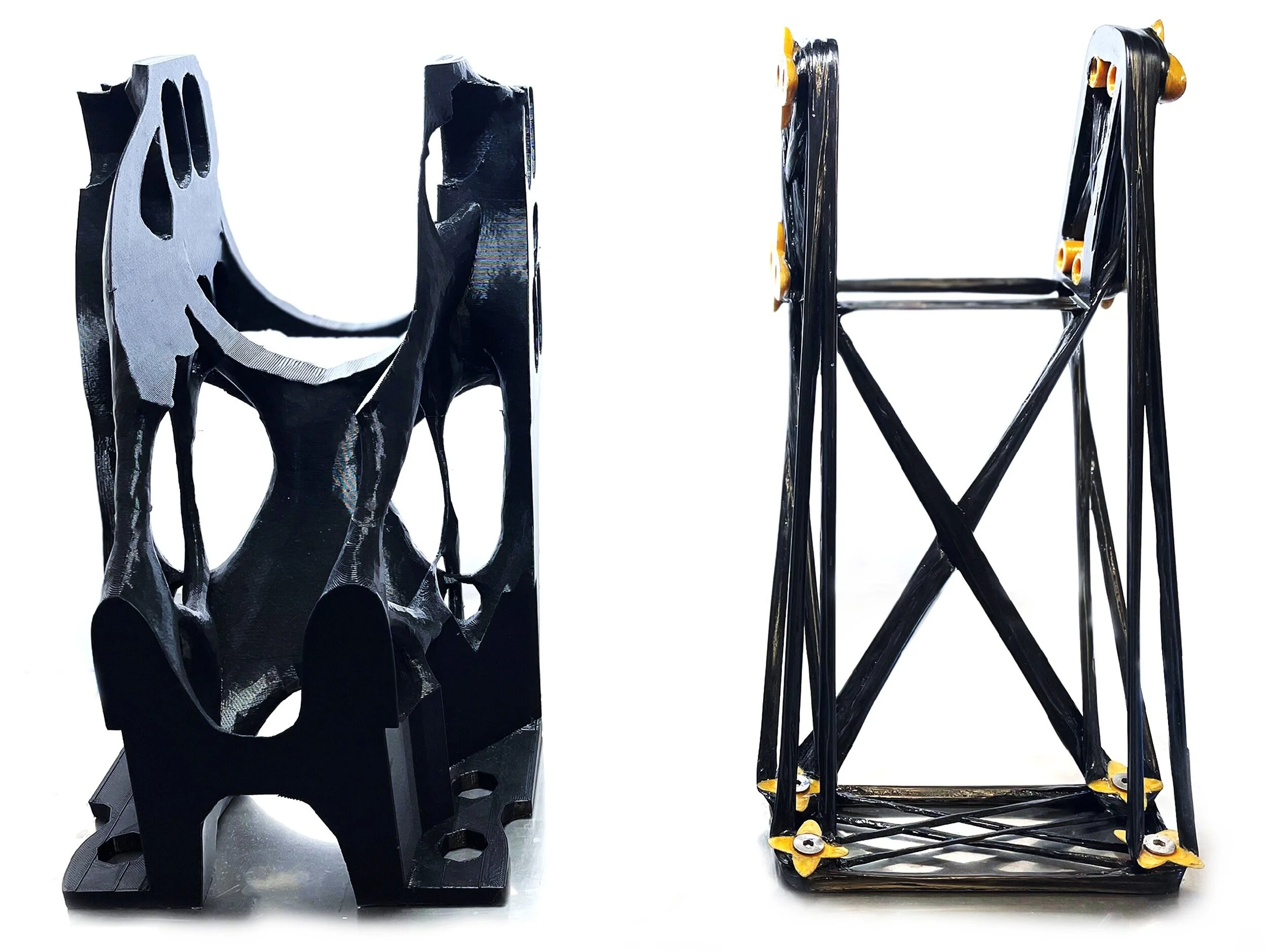